When a compressor fails, production stops. But most failures don’t happen overnight – they build up silently over time. That’s why industrial compressor minor overhauling is more than just a routine fix – it’s a critical strategy to protect plant uptime, reduce energy loss, and avoid major breakdowns.
In this blog, we’ll walk you through the signs that your compressor needs attention, the parts that wear down fastest, and why minor overhauls are one of the smartest maintenance decisions your operations team can make.
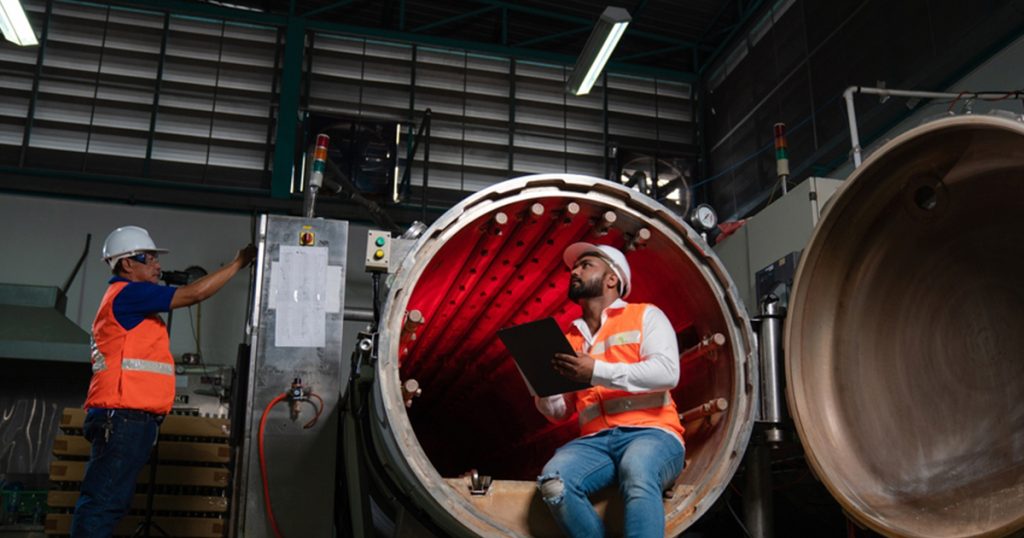
What is the lifespan of an industrial compressor?
The average lifespan of an industrial compressor typically ranges from 15 to 25 years, depending on usage, operating environment, and – most critically – maintenance. Compressors running in harsh environments or without regular care may begin deteriorating much earlier.
Implementing routine servicing like Compressor overhauling maintenance helps extend operational life, maintain efficiency, and reduce unplanned outages. With proper scheduling and inspection protocols, even older compressors can perform reliably for decades.
What is the most common compressor failure?
The most common failure in industrial compressors is overheating – usually caused by poor lubrication, dirty filters, or worn-out components. When systems run too hot for too long, they lose efficiency and start breaking down.
Minor symptoms like increased vibration, air leaks, or pressure drops often go unnoticed until a major failure occurs. That’s why compressor minor overhauling is essential. These smaller-scale interventions allow you to replace worn parts before they cause significant damage.
What is the process for maintaining an air compressor?
Keeping up with air compressor maintenance involves a mix of routine tasks and scheduled overhauls. Some of the core actions include:
- Checking and replacing air filters regularly
- Monitoring oil levels and changing lubricants on time
- Inspecting belts, hoses, and electrical connections
- Testing safety shut-offs and pressure levels
- Cleaning cooling elements to prevent overheating
One key part of the strategy is annual maintenance– a more detailed inspection that goes beyond the basics, ensuring deep component-level health checks.
What parts of the compressor require regular maintenance?
Not all compressor parts wear out equally, but certain components need regular attention to avoid failure. These include:
- Valves and gaskets – prone to leakage
- Bearings and seals – critical for preventing friction and overheating
- Piston rings – especially in reciprocating systems
- Filters and coolers – impact overall performance
- Motor and electrical contacts – crucial for start/stop efficiency
Whether you’re operating a Reciprocating compressor or a centrifugal model, skipping maintenance on these areas can reduce performance dramatically and shorten system lifespan.
Whether it’s compressors, turbines, or pumps, reliable rotary equipment is key to smooth industrial operations. Discover our expert Rotary Equipment Services for precision maintenance and long-term efficiency.
What is the first step in overhauling an air compressor?
The first and most important step is a thorough diagnostic inspection. This involves checking pressure levels, vibration patterns, fluid levels, air quality, and thermal readings. Based on that, technicians can identify whether the overhaul should be minor or major.
During Industrial compressor minor overhauling, only selected components (like seals, gaskets, or filters) are replaced – allowing the unit to stay operational without a full teardown. This step is best taken when early signs of inefficiency show up, before major damage occurs.
Centrifugal and Reciprocating Compressor: Advantages and Main Parts
These are the two most widely used types of compressors in industrial settings, and each has its own set of strengths.
Centrifugal Compressor:
- Advantages: High flow rate, energy-efficient for continuous duty
- Main Parts: Impellers, diffusers, intercoolers, casing
- Ideal For: Large-scale industries with constant airflow demands
Reciprocating Compressor:
- Advantages: High-pressure output, robust for intermittent use
- Main Parts: Pistons, cylinders, crankshaft, valves
- Ideal For: Workshops, smaller plants, or operations needing precise pressure control
Choosing between the two depends on your usage type, but both benefit heavily from Compressor overhauling annual maintenance to ensure lasting performance.
Why Minor Overhauling Matters More Than You Think
Minor overhauling isn’t just a maintenance task – it’s a strategic investment. Unlike a major overhaul that takes your compressor offline for weeks, a Industrial compressor minor overhauling can be done with minimal downtime and at a fraction of the cost.
Benefits include:
- Improved energy efficiency
- Reduced risk of emergency failure
- Better air quality and pressure consistency
- Lower total maintenance cost over time
When done on schedule, it extends your compressor’s life without interrupting your production line.
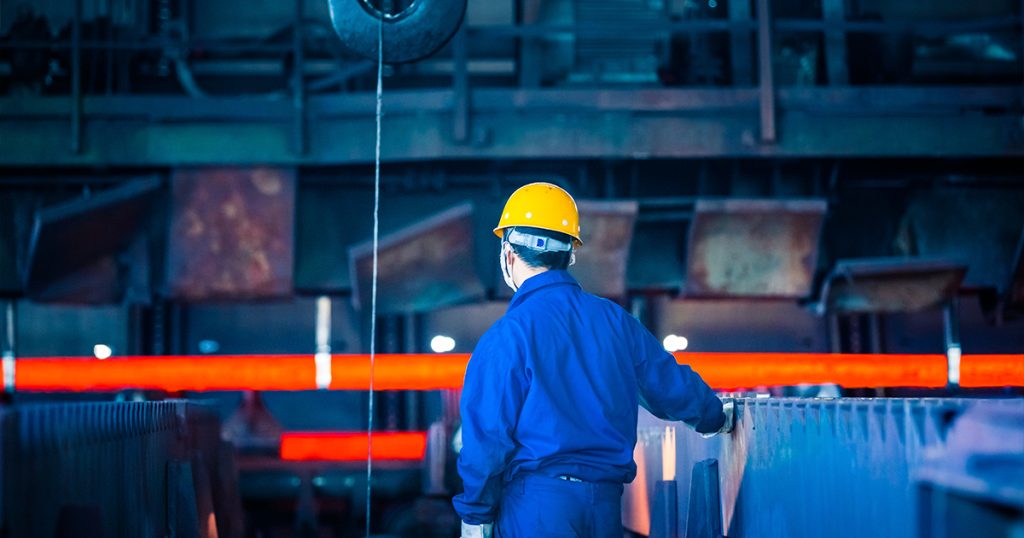
Frequently Asked Questions (FAQs)
Q: How often should industrial compressors be overhauled?
Minor overhauls are typically recommended every 8,000–12,000 hours of operation, depending on your system and environment.
Q: Can I continue operations during minor overhauling?
Yes, in many cases. Minor overhauls can be performed with planned downtime or in shift gaps to avoid production loss.
Q: What’s the difference between minor and major compressor overhauling?
Minor involves component replacements and diagnostics; major includes full disassembly, cleaning, and possible redesign.
Q: Who should perform compressor overhauling?
Always work with trained industrial technicians or certified providers. Overhauls done by untrained staff can create safety risks.
Why Swamina International is Different
At Swamina International, we believe industrial performance is built on reliability – and that begins with proper compressor care. Our expert team provides tailored services from diagnostics to full-scale compressor overhauling, using precision methods and quality components.
Whether you’re managing a large-scale centrifugal system or a high-pressure reciprocating unit, our approach ensures minimal disruption and maximum ROI. In addition to fixing compressors, we also future-proof them.
Final Takeaway: Maintenance Today, Performance Tomorrow
Compressor failure isn’t just a mechanical problem – it’s a production risk, a cost sink, and a preventable issue. If your system is lagging or showing early signs of trouble, don’t wait.
Choose scheduled, expert-led maintenance services to stay ahead of downtime, reduce energy use, and extend your machine’s lifespan. The smartest industrial teams maintain before they repair – and that’s the edge you need in today’s competitive environment.
Want to go deeper into building a reliable overhaul strategy? Explore our in-depth blog on Industrial Compressor Overhauling & Maintenance Strategy to get started.